Наплавка. Классификация способов наплавки
Наплавка — нанесение слоя металла на поверхность заготовки или изделия посредством сварки плавлением. В случае применения для этой цели сварки давлением употребляется термин — наварка (ГОСТ 2601—84). Изготовительная наплавка служит для получения новых биметаллических (многослойных) изделий. Такие изделия состоят из основы (основной металл), обеспечивающей необходимую конструкционную прочность, и наплавленного рабочего слоя (наплавленный металл) с особыми свойствами (износостойкость, термостойкость, коррозионная стойкость и т. д.). Восстановительная наплавка применяется для восстановления первоначальных размеров изношенных или поврежденных деталей. В этом случае наплавленный металл может быть близок по составу и свойствам основному металлу (восстановительная размерная наплавка) или отличаться от них (восстановительная износостойкая наплавка). Наплавленный металл вследствие перемешивания с основным металлом и взаимодействия с атмосферой дуги и шлаком отличается по составу от электродного (присадочного) металла. Доля основного металла в наплавленном слое γ0, обычно выражаемая в процентах, колеблется в широких пределах и зависит от способа и режима наплавки (табл. 25.1). γ0 = F0100/(F0+Fн), (25.1) где F0 — площадь сечения расплавленного основного металла (рис. 25.1); Fн — площадь сечения наплавленного металла. Важной характеристикой процесса является нроизводительность наплавки (см. табл. 25.1), которая измеряется массой металла или площадью поверхности, наплавляемых в единицу времени (кг/ч, м2/ч). Таблица 25.1 Сравнительная характеристика некоторых способов наплавки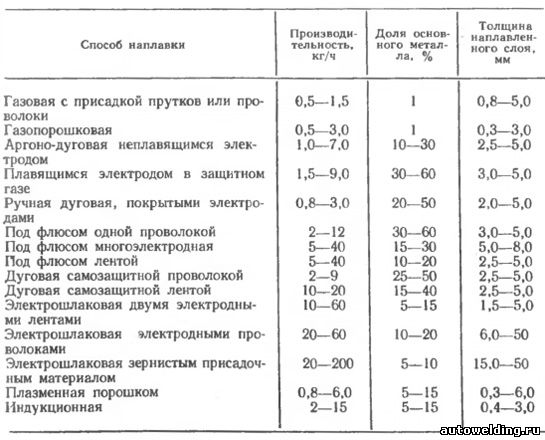
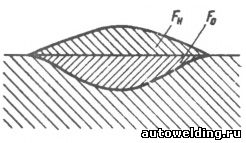
Рис. 25.1. Сечение наплавленного валика: F0 — площадь сечения расплавленного основного металла; Fн — площадь сечения наплавленного металла Классификация способов наплавкиСпособы наплавки, как и способы сварки, классифицируются по трем группам признаков (ГОСТ 19521—74): физическим, техническим и технологическим. По физическому признаку (используемый источник нагрева) основные способы наплавки можно разделить на три группы: - термические (дуговая, электрошлаковая, плазменная, электронно-лучевая, световая, индукционная, газовая, печная);
- термомеханические (контактная, прокаткой, экструдированием);
- механические (взрывом, трением).
Большинство из этих способов в свою очередь могут подразделяться по техническим (способ защиты металла в зоне наплавки, степень механизации наплавки, непрерывность процесса наплавки) и технологическим (по роду тока, по количеству электродов, по наличию внешнего воздействия и т п.) признакам.
|