Оборудование для лазерной резки и технологическая оснастка
Конструктивные схемы машин и комплексов для резки листовДля обработки листов применяют машины и комплексы с микропроцессорным управлением. Комплексы отличаются от машин наличием дополнительных механизмов, обеспечивающих механизацию и автоматизацию вспомогательных операций: загрузки и транспортировки листов в зону резки, разборки,транспортировки и сортировки вырезанных деталей. Более высокая производительность комплекса обусловлена более высоким коэффициентом загрузки машины. В промышленности используются машины трех типов. У портальной машины перемещается портал с технологической оснасткой над неподвижным листом, излучатель СО2-лазера мощностью более 0,5—1 кВт установлен автономно вне портала, излучатель меньшей мощности размещается на портале. У машин второго типа в двух направлениях перемещается обрабатываемый лист, излучатель лазера и технологическая оснастка неподвижны. Типичным представителем машин этого типа является лазер-пресс, сочетающий механическую и лазерную обработку. У машин третьего типа в продольном направлении перемещается обрабатываемый лист, в поперечном — оптический резак по неподвижному порталу. Машины второго и третьего типов применяются, как правило, для резки листов небольших и средних размеров, первого — для резки средних и крупных листов. Типы, основные размеры и параметры, а также общие технические требования к портальным машинам оговорены в ГОСТ 5614—74 и ГОСТ 26940—86. Конструктивные схемы роботов для резки объемных заготовокДля резки заготовок до 1x1x0,5 м, как правило, используют многозвенные роботы с пятью—семью степенями свободы. Обрабатываемая заготовка закрепляется либо на неподвижном столе, либо на столе, имеющем одну—две степени свободы. Излучение подводится к заготовке через систему подвижных зеркал или по волоконным световодам. Заготовки больших габаритов обрабатывают с применением роботов портального типа, у которых раскройный стол, служащий также для закрепления заготовок, может быть неподвижным или иметь одно—два направления линейного перемещения. Излучение к заготовке передается системой подвижных зеркал. Эффективное использование роботов требует механизации и автоматизации вспомогательных операций по транспортировке, загрузке и фиксации заготовок на раскройном столе, а также операций по съему и транспортировке вырезанных деталей. Технологическая оснасткаЭто — система передачи излучения, оптический резак с фокусирующей оптикой и устройством для подачи в зону резки вспомогательного газа, устройство для стабилизации положения фокальной плоскости относительно поверхности заготовки, а также аппаратура для автоматического управления включением излучения и подачи вспомогательного газа. На рис. 28.4 приведены наиболее часто применяющиеся конструктивные схемы оптических резаков. Схемы а—в служат для фокусировки сплошного луча, г и д — для фокусировки полого луча. Наиболее проста схема а на базе фокусирующей линзы, однако ее промышленное применение ограничивается верхним уровнем мощности излучения (1—1,5) кВт. Охлаждаемые зеркальные фокусирующие системы рекомендуется применять при более высоких уровнях мощности излучения. Как правило, зеркальные системы используются с насадками для боковой подачи вспомогательного газа из кольцевого зазора под углом 70—80° к оси луча. 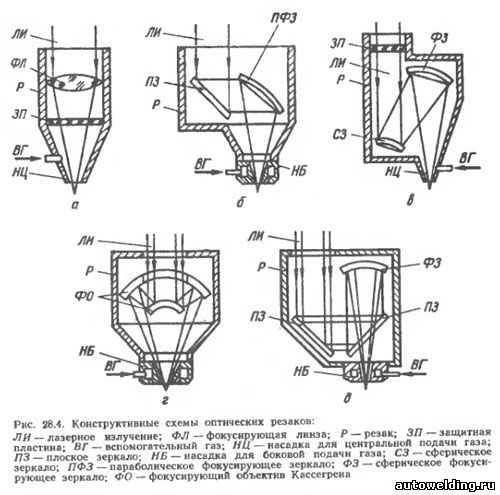
В устройствах для стабилизации положения фокальной плоскости на вертикальной оси используются бесконтактные емкостные и лазерные датчики слежения за поверхностью заготовки, а также электромеханические датчики, опирающиеся на заготовку при ее резке. Производительность оборудованияПроизводительность машин, комплексов и роботов, метры реза в секунду, подсчитывается по формуле: П = knvТvy/[(STvy + SyvT) (n+k—nk)], (28.4) где k — количество одновременно работающих резаков; п — коэффициент загрузки машины; vT — оптимальная технологическая скорость резки, см/с; vy — скорость резки углов и сложных участков контура, см/с; ST, Sy— соответственно длина реза, м, со скоростью vT и vy. В табл. 28.3 приведены результаты расчета производительности оборудования при резке 3-мм стали. В расчетах использовались следующие значения параметров уравнения (28.4): k=1; vT=1,25 см/с при Ризл = =0,25 кВт; vT = 2,9 см/с при Ризл=0,5 кВт и vT = 5,8 см/с при Ризл=1 кВт; ST = 0,7; Sy=0,3.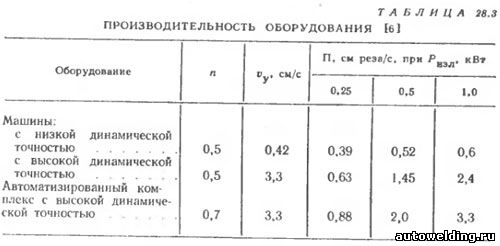
Проанализировав данные табл. 28.3, можно сделать следующие выводы: повышение мощности излучения дает существенный рост производительности лишь при условии увеличения коэффициента загрузки машины и ее динамической точности (жесткости) электромеханического привода; способы повышения коэффициента загрузки — комплексная механизация и автоматизация всех операций, повышение надежности работы оборудования, правильная организация работ при эксплуатации, обслуживании и ремонте оборудования.
|